The Ultimate Guide to Building a Superior ERP System for Food Manufacturing
? Listen to the Summary of this article in Audio
The modern landscape of food and beverage distribution is undergoing a technological metamorphosis, compelling businesses to harmonize with evolving industry demands. In this relentless pursuit of innovation, the best ERP for food manufacturing emerges as the cornerstone for enterprises seeking to fortify their operations. Industry-specific ERP systems are no longer a luxury but a necessity, providing an indispensable framework for food manufacturing compliance and facilitating operations with finesse. These ERP software solutions augment food safety protocols and streamline cost control, while recipe management capabilities ensure products remain consistently at the apex of quality.
The transformational impact of ERP systems in food and beverage domains extends well beyond rudimentary functionalities. With prowess in addressing the intricate facets of food manufacturing compliance, these platforms empower businesses to uphold the highest safety standards, achieving seamless alignment with health regulations. The integration of ERP software solutions amplifies operational efficiency, optimizing the intricate balance between cost control and quality. Meanwhile, robust recipe management tools ensure intellectual property is safeguarded, recipes are perfected, and customer satisfaction remains paramount.
Key Takeaways
- Identify the best ERP for food manufacturing to streamline operations and compliance.
- Employ industry-specific ERP systems for increased precision in managing business functions.
- Ensure stringent food manufacturing compliance with focused ERP software solutions.
- Integrate cost control measures using ERP to maintain financial stability within food safety parameters.
- Use ERP platforms for efficient, secure, and consistent recipe management.
Introduction to ERP and Its Importance in Food Manufacturing
The ever-evolving landscape of the food manufacturing sector posits a multitude of challenges and demands. To navigate these effectively, Enterprise Resource Planning (ERP) has emerged as a linchpin for success. Crafting and utilizing ERP solutions for food manufacturers can address the trifecta of food safety, operational efficiency, and cost management. Given the dynamic nature and stringent compliance requirements of the food industry, an effective food manufacturing ERP system becomes indispensable. Let’s delve into what makes ERP systems so crucial for food manufacturers amid ongoing industry challenges.
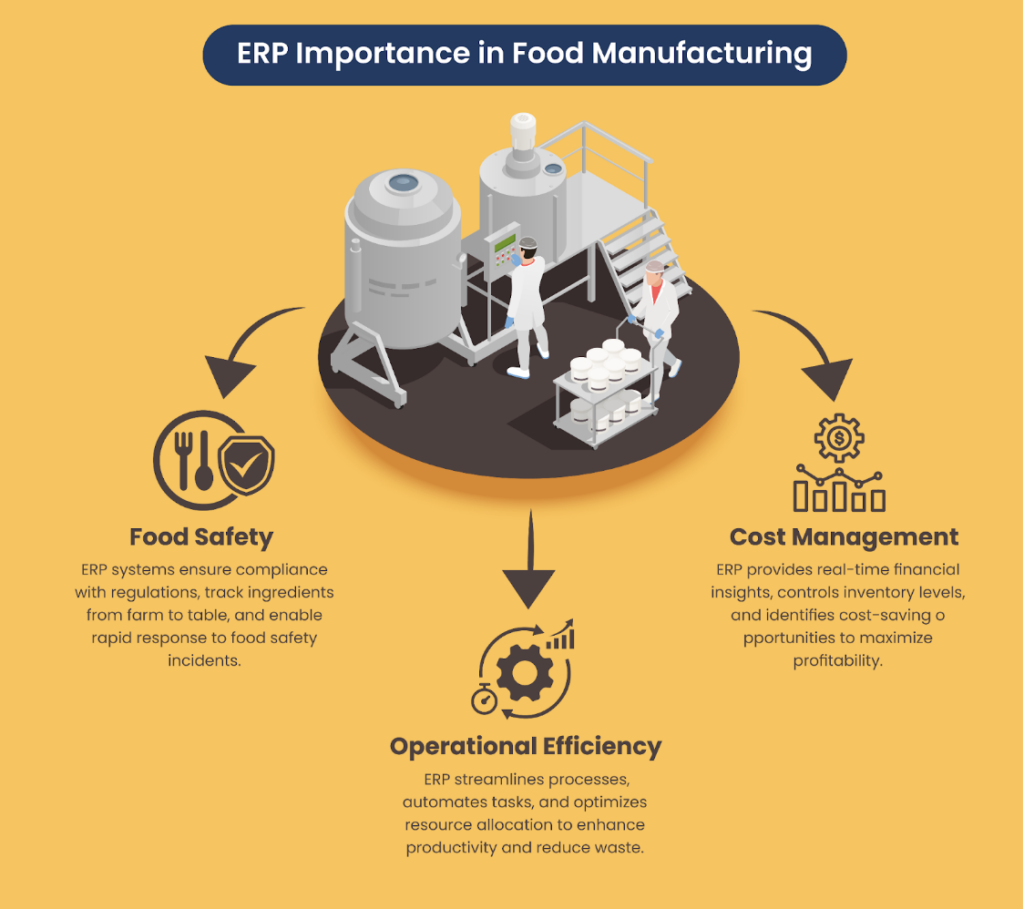
Understanding the Unique Needs of Food Manufacturing Businesses
Food manufacturers operate in a sphere where perishability and stringent regulatory demands for food safety mold their daily operations. Products must adhere to quality standards from the onset of production until they reach the consumer. Changing consumer demands also necessitate a swift response, requiring businesses to adapt continuously. ERP systems for food safety and quality control become critical tools, providing the necessary agility and oversight for businesses to flourish.
Key Features of an Effective Food Manufacturing ERP
An effective food manufacturing ERP bristles with features aimed at simplifying and optimizing complex processes. Among these features are inventory control systems that enhance transparency, food safety modules that ensure adherence to health standards, and warehouse management systems that streamline operations. Real-time data analytics bolster decision-making, while compliance tools make it easier to adhere to regulations like FSMA and HACCP. The synthesis of these features into one robust system defines the core of an effective food manufacturing ERP.
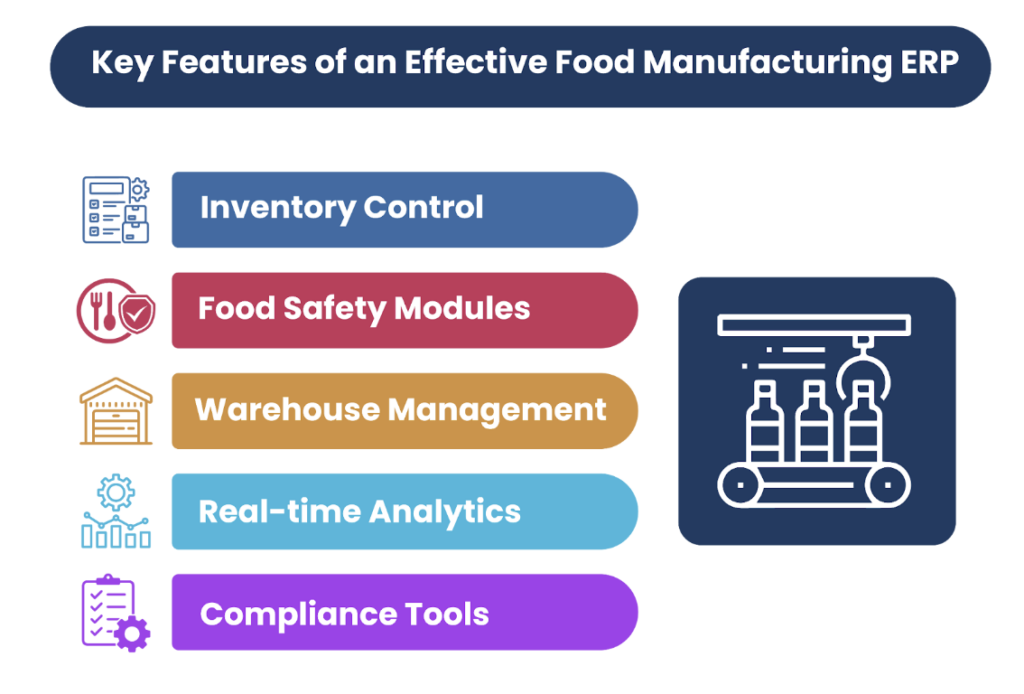
Benefits of Custom ERP Solutions for Food Manufacturers
Custom ERP solutions provide food manufacturers with a tailored approach to confront industry-specific hurdles. With customization, ERP systems can seamlessly integrate disparate business functions, leading to enhanced efficiency and overall productivity. These bespoke solutions afford an end-to-end view of the supply chain, offering actionable insights and enabling compliance with prevailing food safety regulations. Ultimately, the judicious use of ERP systems in the food industry underscores not just the alignment with best practices but also the commitment to innovation and customer satisfaction in a competitive marketplace.
Planning and Strategy: Laying the Groundwork for Your ERP
In strategizing the implementation of an ERP system, careful planning becomes an indispensable precursor to success. Food manufacturing companies ought to delineate their ERP planning strategy meticulously to ensure the system fulfills all food manufacturing business requirements. The process begins with a deep understanding of the business’s unique needs, followed by the selection of an adept ERP development partner, and concludes with a comprehensive approach to ERP budget and resources management. Such proactive ERP implementation strategy planning is imperative for aligning technological solutions with operational goals.
Identifying Your Business Requirements
Firmly grasping the specific needs and challenges of a food manufacturing enterprise is paramount. From supply chain logistics to recipe management, every piece of the ERP puzzle must fit into the broader organizational framework and cater to the market’s demand for safety and efficiency. Crafting a customized ERP system starts with an intricate understanding of these needs.
Selecting the Right ERP Development Partner
The alliance with a fitting ERP development partner is critical to the project’s triumph. It is essential that the chosen partner not only provides scalable ERP solutions like ASCTrac® WMS but also brings expertise and deep industry knowledge. Integration capabilities, paired with steadfast support, manifest as vital aspects of this partnership, laying a foundation for seamless system functionality.
Establishing Budget and Resource Allocation
Financial planning cannot be overlooked when undertaking an ERP project. Resource allocation goes hand in hand with ERP budgeting, ensuring that the chosen solution aligns with the company’s financial constraints while delivering on the promise of efficiency. It warrants a strategic financial layout to cover all phases, from development and implementation to training and maintenance.
ERP Planning Phase | Resources Required | Projected Costs | Goals and Outcomes |
---|---|---|---|
Initial Assessment | Consultation, Industry Analysis | Varies with Scope | Clear Understanding of ERP Needs |
Partner Selection | Partner Evaluation, Proposal Comparison | Project Proposals Evaluation | Selection of Competent ERP Partner |
Development | Technical Team, Software Tools | Development Costs | Customized ERP Framework |
Implementation | Training Programs, User Manuals | Implementation Resources | Smooth ERP Integration and User Adaptation |
Post-Launch | Ongoing Support, System Updates | Support and Maintenance Costs | Sustained ERP Performance and Scalability |
An ERP system in the competitive landscape of food manufacturing is no small endeavor, and its successful deployment is reliant on disciplined and strategic foresight. A company’s commitment to thoughtful ERP planning underscores its dedication to staying at the forefront of technological advancements while enhancing business operations and meeting industry regulations.
Our team of ERP experts can help you plan and implement a tailored ERP solution that streamlines your food manufacturing processes and ensures compliance.
Design and Customization: Tailoring the ERP to Your Business
When it comes to ERP design customization within the food manufacturing industry, incorporating a system that’s tailored to the unique needs of the business is paramount for streamlined operations and sustained competitiveness. A fully customized ERP aligns closely with the company’s established ERP workflows, advancing operational efficiency, and reinforcing compliance quality control in ERP systems. The attention to design details facilitates ERP supply chain integration and leverages ERP data analytics that drive intelligent, nimble business decisions.
Customizing Workflows for Food Manufacturing Processes
Effective ERP systems in food manufacturing hinge upon workflows that mirror the rhythm and requirements of the production floor. Customized workflows reduce bottlenecks and expedite processes ranging from procurement to production, ensuring agility and precision throughout the food manufacturing lifecycle. These workflows, when thoughtfully designed, not only harmonize operations but also reduce waste, optimize resource allocation, and support continuous improvement in efficiency and productivity.
Incorporating Compliance and Quality Control Modules
Guaranteeing compliance with industry regulations and maintaining strict quality control measures is not merely about adherence to standards – it’s about customer trust and product integrity. Modules designed to manage compliance augment the ERP’s capability to keep pace with ever-evolving regulations, such as FSMA and HACCP standards. Simultaneously, quality control modules integrated into the ERP system perform continuous monitoring and verification, creating an audit trail and facilitating product consistency across batches.
Integrating Supply Chain Management for Efficiency
The backbone of any food manufacturing operation lies in its supply chain. By weaving supply chain management seamlessly into the ERP infrastructure, businesses gain an end-to-end view of their operations. This integration supports timely and informed decision-making, from managing inventory levels to coordinating logistics and responding to market demands – all while minimizing disruptions and maintaining a graceful flow of goods and information.
Leveraging Data Analytics and Reporting
Data is the currency of decision-making in the digital era. An ERP system enriched with data analytics tools translates vast quantities of data into actionable insights. Through real-time reporting and comprehensive analytics, food manufacturers can discern patterns, forecast demands, and assess the efficacy of operations. These analytics capabilities enable proactive adjustments and strategic planning that underpin a competitive edge in a fast-moving market.
Technology Considerations for ERP Development
Embarking on the journey of ERP development in food manufacturing is akin to constructing a state-of-the-art facility; it demands extreme precision and forethought in technological considerations. The chosen technological infrastructure serves as the blueprint that will define the efficiency, scalability, and security of the ERP system. It is imperative to make informed decisions concerning ERP software architecture, cloud computing integration, and adherence to stringent security protocols to ensure the ERP system’s endurance and resilience in the face of the industry’s dynamic nature.
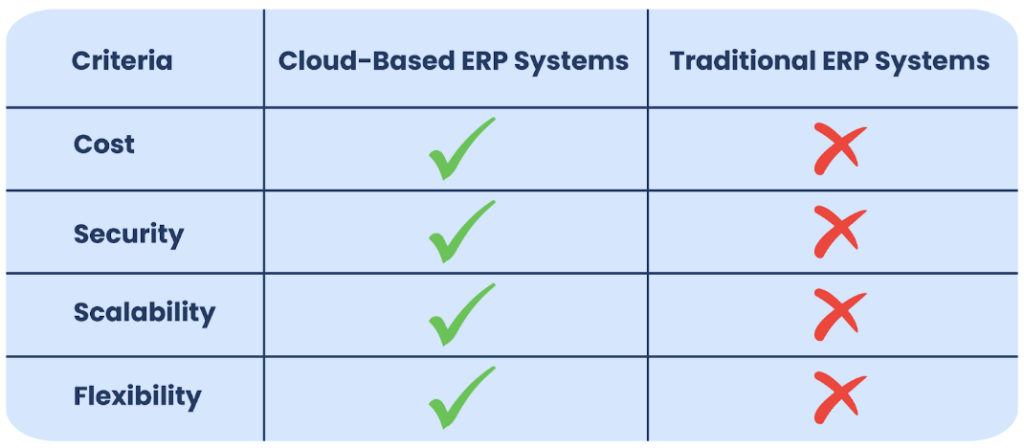
Choosing the Right Software Architecture and Platform
Selecting the optimal ERP software architecture is a pivotal decision that sets the stage for future scalability and customization. An architecturally sound ERP system should be both robust and flexible, accommodating the growth of the food manufacturing business without necessitating a complete system overhaul. Focusing on modularity within the architecture allows for individual components to be updated or replaced as needed, thereby future-proofing the ERP solution against emergent technologies and market shifts.
The Role of Cloud Computing in ERP Solutions
Cloud computing has radically shifted the ERP landscape, delivering enhanced accessibility and a level of flexibility previously unattainable for food manufacturers. Cloud-based ERP solutions dispense with the need for substantial upfront hardware investments while enabling seamless, on-the-go access to data and core business functions. Moreover, the cloud’s capability to automatically apply updates ensures that the ERP system remains perpetually at the frontier of technological innovation.
Security in Food Manufacturing ERP Systems
The sanctity of data within food manufacturing operations cannot be overstated, making ERP system security a paramount concern. ERP providers must embed advanced security measures within the system’s framework, diligently safeguarding sensitive food production and distribution data. These measures must comply with rigorous government regulations and industry standards, fostering an impenetrable digital environment for all stakeholders.
Mobile Accessibility and IoT Integration
ERP mobile accessibility has emerged as a significant contributor to operational dexterity in food manufacturing. By enabling real-time data access from any location, ERP systems support swift decision-making and heightened productivity. Additionally, with the advent of the Internet of Things (IoT), ERP systems can now integrate with a myriad of devices and sensors, offering unparalleled real-time insights and a fertile ground for advanced analytics and automation within the intricacies of food manufacturing.
Implementation and Training: Ensuring a Smooth Transition
Recognizing that the implementation phase is as strategic as the ERP system’s design itself, the ultimate success of an ERP launch hinges on meticulous planning and preparation. A well-orchestrated ERP implementation and comprehensive staff training can serve as the catalyst for transformative operational efficiency and seamless integration into existing company processes. To this end, food manufacturing entities embarking on this digital evolution must consider phased strategies and robust training programs in tandem with organizational change management practices.
Developing a Phased Implementation Approach
The adoption of a phased ERP approach permits an organization to manage the transition incrementally, minimizing disruption while allowing room for continuous assessment and adaptation. Setting in motion a clearly charted implementation timeline with defined stages enables businesses to test and refine ERP system functionalities, ensuring that each phase endows users with the confidence and tools necessary for the next. This approach not only stages the complexity of the rollout but also elevates the likelihood of a harmonious enterprise-wide assimilation of the new ERP system.
Training Your Staff for Optimal ERP Usage
To unlock the full potential of an ERP system, ERP staff training is indispensable. Through a structured and interactive training curriculum, employees are equipped with the knowledge and skills necessary to leverage the ERP effectively. A comprehensive training agenda should cover critical aspects of the software, blending various educational methods such as workshops, practical exercises, and e-learning modules. By investing in extensive ERP training, an organization empowers its workforce to harness the power of the ERP solution, driving productivity and innovation.
Managing Change in the Organization
Implementing a new ERP system entails a significant shift in the existing operational milieu, necessitating proactive organizational change management ERP strategies. By actively engaging with stakeholders at all levels, addressing concerns, and reinforcing the benefits of change, businesses can foster a supportive environment conducive to the transition. Regular communication, agility in addressing feedback, and celebrating milestones are quintessential in cultivating a culture that not only accepts but also champions the new system. Central to this endeavor is the recognition that people are at the heart of change, and their alignment is integral to the success of any ERP implementation.
Ultimately, a thoughtfully executed ERP implementation strategy coupled with persuasive change management practices can catapult an organization towards heightened operational efficacy and competitive prowess. By laying the groundwork for refined business processes and data-driven decisions, ERP systems stand as pivotal solutions in the rapidly advancing realm of food manufacturing.
From workflow optimization to compliance modules, our developers can create a fully customized ERP system that aligns with your unique business needs.
Ongoing Support and Maintenance
For food manufacturing operations, the integration of an ERP system is just the beginning. As the industry landscape evolves and businesses grow, the systems that drive success must keep pace through diligent ERP support and maintenance. Striking the balance between innovation and stability, an ERP’s ability to adapt is contingent upon the robustness of its support structure and the proactive management of its evolution.
Establishing an Effective ERP Support System
Effective ERP support and maintenance serve as the backbone to ensuring that food manufacturing businesses can optimally use their ERP systems. A dedicated support team is crucial not only for resolving immediate technical issues but also for providing the expertise to enhance system capabilities progressively. Establishing an effective ERP support system involves rigorous vendor assessment, forging partnerships with experienced providers like Panni Management, which specializes in Sage X3 ERP solutions, and ensuring that hands-on training is readily available to empower users to fully leverage ERP functionalities.
Planning for Regular Updates and Upgrades
Keeping an ERP system at the forefront of technology necessitates a structured plan for routine ERP updates and upgrades. This proactive stance ensures that the ERP can handle emerging industry demands, new regulatory requirements, and technological advancements. Regular upgrade schedules contribute to enhanced system reliability, preserving the ERP’s role as a cornerstone of operational success.
Monitoring ERP System Performance and User Feedback
Continuous ERP performance monitoring is essential for capturing real-time insights into system operations and user engagement. Performance metrics are invaluable for detecting inefficiencies and guiding optimization efforts. Gathering and analyzing ERP system feedback from users becomes a pivotal process for identifying areas of improvement. Intertwining user feedback with performance data catalyzes the evolution of an ERP system, ensuring it remains finely tuned to the distinctive needs of food and beverage businesses.
In conclusion, a robust strategy for ERP support and maintenance is vital for maintaining the system’s relevance and reliability within the demanding realm of food manufacturing. The successful sustainment of an ERP relies on a synchronized effort to provide consistent support, implement periodic updates, and vigilantly monitor system performance while valuing user feedback. By securing these pillars of ongoing support and maintenance, manufacturers can expect their ERP investments to yield continued efficiency, adaptability, and competitive advantage.
Measuring the Success of Your Food Manufacturing ERP
Within the dynamic sphere of food manufacturing, an Enterprise Resource Planning (ERP) system plays a critical role. However, to truly understand its value, one must delve deeply into success metrics ERP, evaluating key performance indicators (KPIs) and the return on investment (ROI). This process ensures that the ERP not just exists as an operational tool but functions effectively in driving business growth and efficiency.
Defining KPIs for Your ERP System
Setting up specific and measurable metrics is crucial for an accurate ERP system success evaluation. KPIs act as benchmarks for performance, offering insight into various aspects of the ERP’s effectiveness. Common KPIs include inventory turnover rates, order fulfillment accuracy, and production cycle times. By defining ERP KPIs, organizations can monitor their system’s efficacy in real-time, make informed decisions, and identify opportunities to enhance productivity and reduce operational costs.
- Inventory accuracy and turnover ratio: Reflects the effectiveness of inventory management and the frequency of stock replenishment.
- On-time delivery rate: Indicates the system’s success in managing supply chain and logistics to meet delivery schedules.
- Cost savings from process improvements: Captures the reduction in expenses due to increased ERP-driven operational efficiencies.
- Customer satisfaction and retention rates: Measures the impact of ERP on customer service and long-term client relationships.
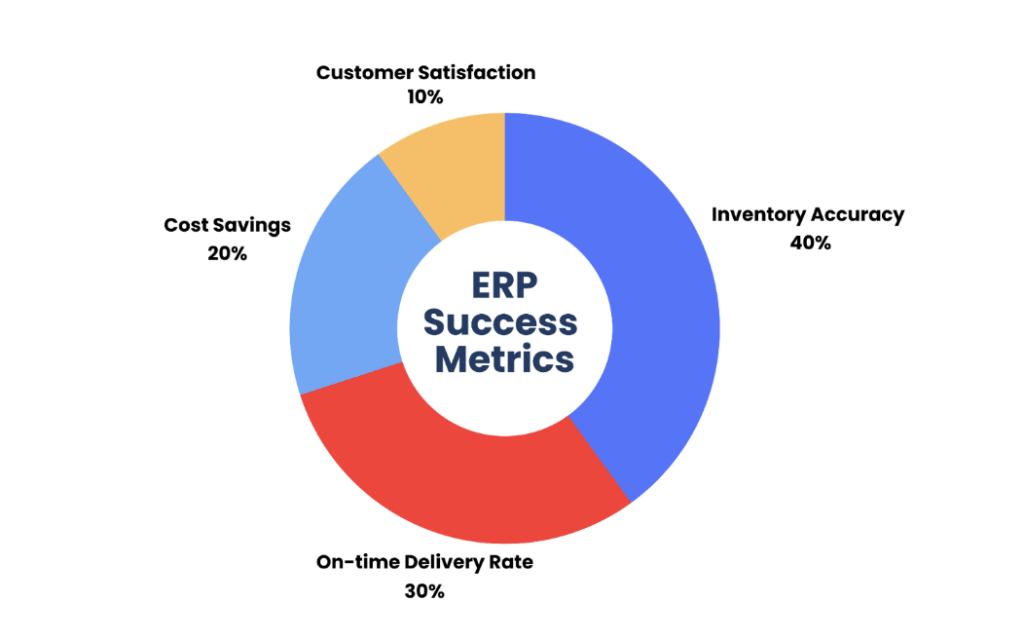
Analyzing ROI of Your ERP Investment
Determining ERP investment ROI involves examining both qualitative and quantitative factors, including initial costs, ongoing operating expenses, and the tangible benefits realized over time. To facilitate this analysis, companies assess improvements in process efficiencies, reductions in overheads, and better decision-making capabilities provided by the system. The financial analysis should encapsulate the total cost of ownership (TCO) correlated against value-added operational outcomes such as increased production throughput or enhanced customer experiences.
ROI Component | Pre-ERP Scenario | Post-ERP Implementation | Impact Analysis |
---|---|---|---|
Operational Efficiency | Baseline data | Improved process times | Percentage increase in efficiency |
Inventory Management | Higher holding costs | Reduced inventory levels | Cost savings achieved |
Cost of Operations | Existing operating expenses | Post-implementation expenses | Total cost reduction |
Revenue Growth | Stagnant or slow growth | Increased sales or market share | Percentage growth in revenue |
Thoroughly scrutinizing these metrics and performing often evaluation against pre-set targets offers a clear portrait of whether the ERP investment is on the path to paying dividends. Consequently, recurrent review of these success metrics and refinement of strategies based on data is essential to align the ERP system continually with overarching business goals.
Conclusion: Sustaining Growth with Your Custom ERP Solution
The strategic embrace of a custom ERP system marks a pivotal commitment to sustaining growth ERP in the competitive realm of food manufacturing. Like an astute navigator in uncharted waters, a well-integrated ERP solution maps the course for operational excellence, making it an essential compass for businesses maneuvering the complexities of the food industry landscape. The success of such ERP-driven food manufacturing businesses hinges on the pillars of meticulous ERP selection, tailored customization, and relentless pursuit of innovation. These foundational aspects secure not only the system’s longevity but also the vitality and scalability of the business itself.
Ensuring ERP system longevity means preparing for the future while addressing the needs of the present. A custom ERP system becomes the backbone of enterprise agility, equipped to evolve with the industry’s rapid technological and regulatory shifts. With its robust framework, a tailored ERP system supports proactive operations and competent responses to emerging challenges and market demands. The fusion of flexibility and dependability inherent in these systems empowers businesses to consistently deliver high-quality products, underscore their commitment to food safety, and maintain unwavering customer satisfaction.
Adeptly steering through the volatile currents of the food manufacturing sector requires a steady hand and an ERP system that can withstand the tempests of change. Embodying the insights and strategies presented in this guide establishes a fortified platform for ERP-driven food manufacturing success. By nurturing a culture that values continuous improvement and strategic adaptation, a custom ERP system is not merely an operational tool — it becomes the catalyst for enduring innovation, stability, and growth in this ever-evolving industry.
Partner with our experts to ensure your food manufacturing ERP system delivers measurable results and a strong return on investment.
FAQ
What makes an ERP solution suitable for food manufacturing?
An ERP solution tailored for food manufacturing must include features for industry-specific requirements such as food safety, compliance, cost control, and recipe management. It should enable tracking of production processes, adherence to expiration and compliance standards, and provide specialized reporting to mitigate risks associated with food recalls.
How do ERP systems help with food safety and compliance?
ERP systems help by automating critical processes. They offer robust warehouse management, real-time traceability, and inventory control tailored to the food industry’s needs. They provide tools to ensure compliance with regulations like FSMA and HACCP and enable manufacturers to maintain high food safety and quality control standards.
What should be considered when planning an ERP implementation for food manufacturing?
When planning for ERP implementation, businesses should clearly define their requirements, select the right ERP development partner, establish a realistic budget, allocate adequate resources, and devise a strategy that aligns with their overall business goals for a well-coordinated rollout.
How can workflow customization in an ERP enhance food manufacturing processes?
Customizing workflows for food manufacturing processes ensures that the ERP system reflects the specific operational procedures of the company. It guarantees compliance, enhances efficiency, and maintains quality control across the supply chain, meeting the unique challenges of the industry.
Why is cloud computing beneficial for an ERP solution in food manufacturing?
Cloud computing offers several benefits for food manufacturing ERP solutions, including cost savings, enhanced accessibility, operational flexibility, automatic updates, and the ability to effortlessly scale in response to business growth. Cloud deployments also facilitate remote access and can streamline the integration of new technologies as needed.
How important is staff training in the process of ERP implementation?
Staff training is crucial during ERP implementation, as it ensures that employees are competent in using the new system effectively. Comprehensive training enhances user adoption, minimizes resistance to change, and helps in realizing the full potential of the ERP to optimize business operations.
What does ongoing support and maintenance entail for an ERP system?
Ongoing support and maintenance involve establishing a reliable support system, planning for routine updates and upgrades to the software, and actively monitoring performance. Processing user feedback is also key to successful ongoing maintenance, ensuring the ERP adapts to changing needs and continues to improve over time.
How should the success of an ERP system in a food manufacturing setting be measured?
Success should be measured using well-defined Key Performance Indicators (KPIs) that match the company’s objectives. It’s important to analyze the ERP’s Return on Investment (ROI) by assessing efficiency improvements, cost reductions, and decision-making capabilities to ensure the system aligns with long-term business goals.